In an era where digital transformation is revolutionizing industries, the concept of a “Digital Twin” has emerged as a critical player. But what is a digital twin? Simply put, a digital twin represents a real-world physical product, system, or process.
It is an almost indistinguishable digital counterpart for practical purposes such as simulation, integration, testing, monitoring, and maintenance. This technology is disrupting traditional methods and paving the way for more efficient, cost-effective, and innovative solutions.
Contents
What Is A Digital Twin?
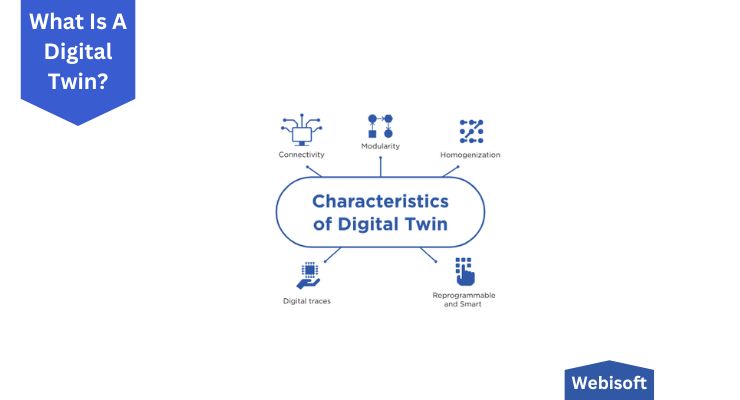
A digital twin is dynamic. It is the physical object or system’s virtual replica. It mirrors the real-world entity, reflecting its current state, behavior, and performance. This digital counterpart is not just a static model.
It evolves and changes in real time as its physical counterpart experiences changes. The creation of a digital twin involves the integration of data from various sources.
These data sources can include sensors embedded in the physical object, external environmental data, and operational data. The data is then processed and visualized to create a dynamic, real-time digital representation of the physical object.
The digital twin concept is rooted in systems engineering. It has been greatly facilitated by technological advancements such as the IoT, cloud computing, data analytics, and machine learning.
These technologies enable the real-time collection, processing, and analysis of vast amounts of data essential for creating and operating digital twins.
Digital twins serve multiple purposes. They can be used for monitoring, where the state and performance of the physical object are continuously tracked.
This can help identify any issues or anomalies in real-time, enabling proactive maintenance and preventing potential failures. Digital twins can also be used for simulation and testing.
Different scenarios can be simulated on the digital twin without any risk to the physical object. This can help understand how the object would respond under different conditions, test new operational strategies, and make informed decisions.
Furthermore, digital twins can be crucial in designing and developing new products or systems. They can simulate and test different design options, understand their implications, and optimize the design before it is physically built.
This can significantly reduce the time, cost, and risk associated with the development process.
How Does A Digital Twin Work?
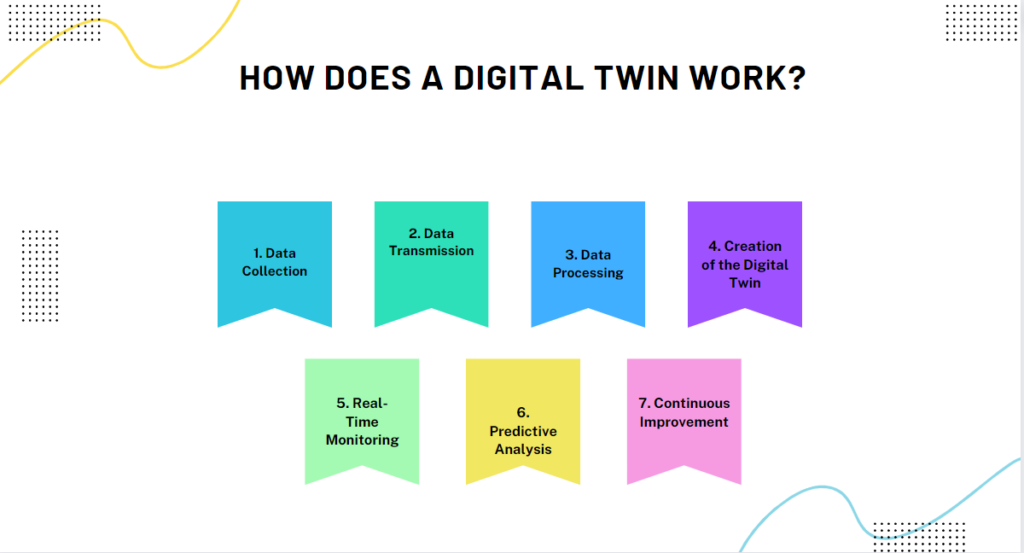
Digital twins collect real-time data from sensors placed on the physical entity. This data is then processed and presented in a digital platform, creating a real-time digital counterpart of the physical entity.
This allows for real-time monitoring, analysis, and even prediction of future performance. The operation of a digital twin is a fascinating process combining data, connectivity, and advanced analytics.
Let’s delve deeper into how a digital twin works.
1. Data Collection
The first step in operating a digital twin is data collection. Sensors attached to the physical entity gather real-time data about various parameters.
This could include temperature, pressure, speed, and more. The type of data collected depends on the nature of the physical entity and the purpose of the digital twin.
2. Data Transmission
Once the data is collected, it must be transmitted to a digital platform. This is where connectivity technologies such as the Internet of Things (IoT) come into play.
The IoT enables seamless and real-time data transfer from the physical entity to the digital platform.
3. Data Processing and Analysis
Upon reaching the digital platform, the data undergoes processing and analysis. Advanced analytics techniques are used to process the data and extract meaningful insights.
These insights can provide valuable information about the current state and performance of the physical entity.
4. Creation of the Digital Twin
The processed data is then used to create a real-time digital representation of the physical entity. This digital representation mirrors the physical entity’s state, behavior, and performance in the real world.
It provides a virtual platform where the physical entity can be monitored, analyzed, and even manipulated without interacting with the actual entity.
5. Real-Time Monitoring
One of the critical features of a digital twin is its ability to provide real-time monitoring. The digital twin updates continuously as new data is collected from the physical entity.
It allows for real-time tracking of the state and performance of the physical entity. Any changes in the physical entity are immediately reflected in the digital twin.
6. Predictive Analysis
Beyond real-time monitoring, digital twins also enable predictive analysis. By analyzing historical and real-time data, predictive models can be built to forecast future performance and detect potential issues.
This predictive capability can be invaluable in preventing failures, optimizing performance, and planning maintenance activities.
7. Continuous Improvement
The operation of a digital twin is continuous. The digital twin becomes more accurate and valuable as more data is collected and analyzed.
This continuous improvement allows the digital twin to adapt to changes in the physical entity and the environment, making it a dynamic and evolving tool.
How To Create A Digital Twin?
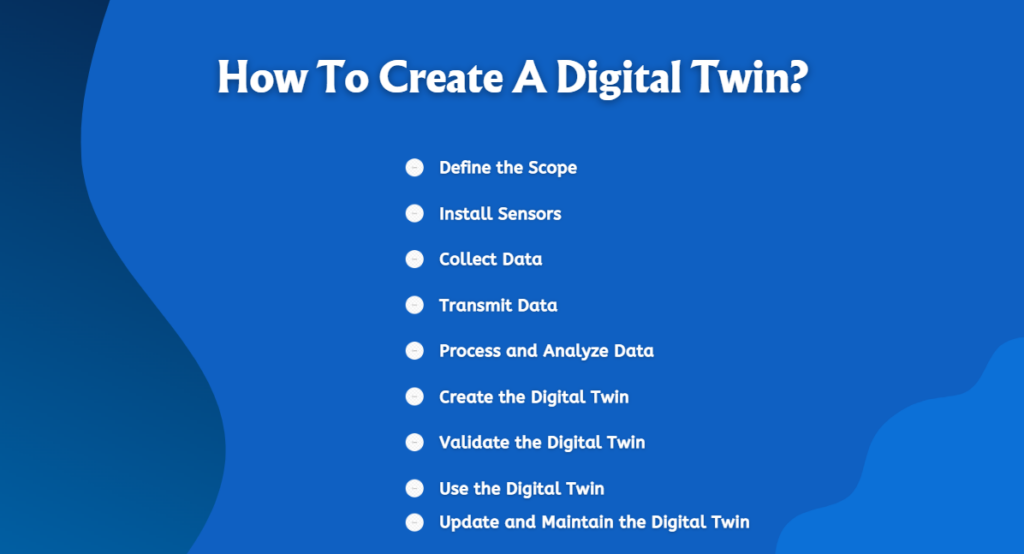
Creating a digital twin involves several steps. First, sensors are installed on the physical entity to collect necessary data.
This data is then integrated into a digital platform where it is processed and visualized. The digital twin is then ready to be used for monitoring, analysis, and prediction purposes.
1. Define the Scope
The first step in creating a digital twin is defining the project’s scope. This involves identifying the physical entity that will be twinned and understanding its essential characteristics and behaviors.
The scope should be clearly specified to ensure the digital twin accurately represents the physical entity.
This might involve detailed discussions with stakeholders, a thorough review of the entity’s specifications, and a clear understanding of the goals and objectives of the digital twin.
2. Install Sensors
Once the scope is defined, sensors are installed on the physical entity. These sensors collect real-time data about various parameters such as temperature, pressure, and speed.
The type and number of sensors depend on the nature of the physical entity and the data requirements of the digital twin. The installation of sensors should be done carefully to ensure that they are correctly positioned and calibrated to collect accurate data.
3. Collect Data
The sensors collect data from the physical entity in real time. This data forms the basis for creating and operating the digital twin. The data collection process should be carefully managed to ensure that the data is accurate and reliable.
This might involve regular checks and calibrations of the sensors, as well as the use of data validation techniques to ensure the quality of the data.
4. Transmit Data
The collected data is transmitted to a digital platform. This is facilitated by connectivity technologies such as the Internet of Things (IoT). The IoT enables seamless and real-time data transfer from the physical entity to the digital platform.
The data transmission should be secure and reliable to prevent data loss or corruption.
5. Process and Analyze Data
Upon reaching the digital platform, the data undergoes processing and analysis. Advanced analytics techniques contain machine learning and artificial intelligence.
These are used to process the data and extract meaningful insights. These insights can provide valuable information about the current state and performance of the physical entity.
The data processing and analysis should be done using robust and reliable analytics tools to ensure the accuracy and reliability of the insights.
6. Create the Digital Twin
The processed data is then used to create a real-time digital representation of the physical entity. This digital representation mirrors the physical entity’s state, behavior, and performance in the real world.
It provides a virtual platform where the physical entity can be monitored, analyzed, and even manipulated without interacting with the actual entity.
The digital twin creation should be done using advanced digital twin technologies to ensure that the digital twin is accurate and realistic.
7. Validate the Digital Twin
Once the digital twin is created, it must be validated to ensure it accurately represents the physical entity. This involves comparing the digital twin’s performance with the physical entity’s actual performance.
Any discrepancies should be identified and addressed. The validation process should be thorough and rigorous to ensure the accuracy and reliability of the digital twin.
8. Use the Digital Twin
Once validated, the digital twin is ready for various purposes, such as monitoring, analysis, and prediction.
The digital twin offers valuable insights that can help make informed decisions, optimize performance, and prevent potential issues. The digital twin should be carefully managed to be used effectively and responsibly.
9. Update and Maintain the Digital Twin
It should be regularly maintained to ensure it accurately represents the physical entity. This involves updating the digital twin as changes occur in the physical entity and maintaining the data collection, transmission, and processing systems.
The update and maintenance process should be proactive and systematic to ensure the long-term effectiveness and reliability of the digital twin. Creating a digital twin is a complex but rewarding process.
With careful planning and execution, a digital twin can provide valuable insights and benefits that can significantly enhance the physical entity’s understanding, management, and optimization.
A Five-Level Digital Twin Taxonomy
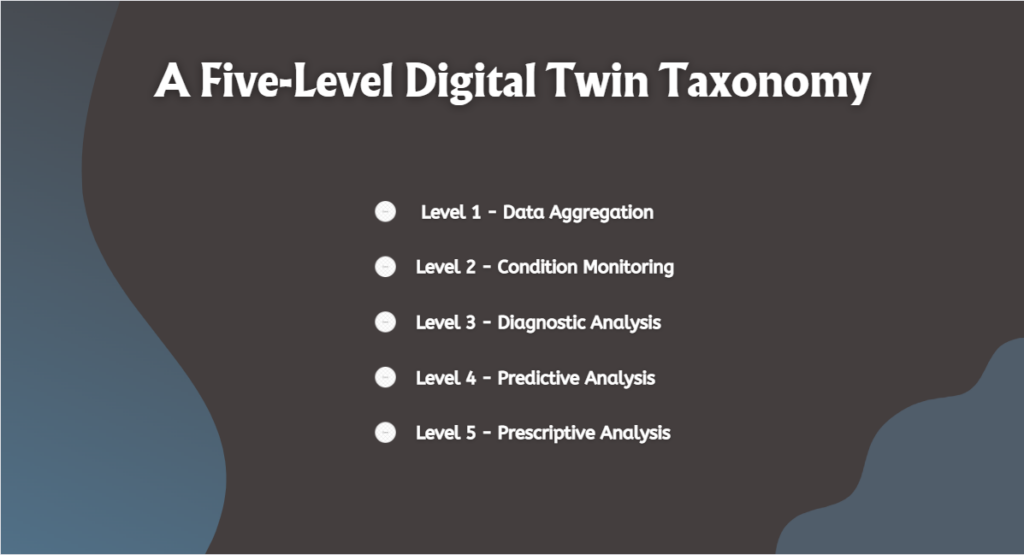
Digital twins, the virtual replicas of physical entities, have revolutionized how we understand, monitor, and optimize our physical world.
They offer a different unique blend of physical and digital, enabling us to gain unprecedented insights into our systems, processes, and products.
But not all digital twins are created equal. They vary in complexity and functionality, leading to a five-level taxonomy that helps us better understand and categorize them. Let’s delve deeper into each level:
1. Level 1 – Data Aggregation
A digital twin serves as a data aggregator at the most basic level. It collects and compiles data from the physical entity, providing a consolidated view of various parameters.
This level is primarily about data collection and aggregation, laying the foundation for more advanced functionalities.
2. Level 2 – Condition Monitoring
The second level of digital twin taxonomy involves condition monitoring. Here, the digital twin not only collects data but also monitors the condition of the physical entity in real time.
This allows for immediate detection of anomalies or deviations, enabling prompt action to mitigate potential issues.
3. Level 3 – Diagnostic Analysis
At the third level, the digital twin takes a step further by diagnosing issues based on the collected data.
It analyzes the data to identify the root cause of any detected anomalies, providing valuable insights into the underlying issues. This diagnostic capability enhances problem-solving, making it more efficient and effective.
4. Level 4 – Predictive Analysis
The fourth level of digital twin taxonomy involves predictive analysis. Here, the digital twin uses advanced analytics techniques to predict future performance and detect potential issues before they occur.
This predictive capability enables proactive management of the physical entity, preventing issues before they happen and optimizing performance for better outcomes.
5. Level 5 – Prescriptive Analysis
At the highest level, the digital twin provides prescriptive analysis. It goes beyond diagnosing and predicting to providing recommendations for optimizing performance and mitigating issues.
This prescriptive capability transforms the digital twin from a passive observer to an active participant, offering actionable insights for decision-making.
This five-level taxonomy provides a comprehensive framework for understanding and categorizing digital twins. It highlights the progressive increase in complexity and functionality, from primary data aggregation to advanced prescriptive analysis.
The digital twin becomes more sophisticated as we move up the levels, offering more value and insights.
However, it also requires more advanced technologies and capabilities, making it essential to choose the right level based on the specific needs and capabilities of the organization.
What Are the Applications of Digital Twins?
Digital twins, a revolutionary concept in technology, are virtual replicas of physical entities, systems, or processes. They bridge the physical and digital worlds, enabling real-time monitoring, simulation, and analysis.
The applications of digital twins are vast and varied, spanning numerous sectors, from manufacturing to healthcare and urban planning. In the manufacturing industry, digital twins are transforming the way businesses operate.
They are a powerful tool for real-time monitoring equipment, capturing performance, wear and tear data, and overall operational efficiency. This data-driven approach allows for predictive maintenance.
These potential problems can be identified and addressed before they escalate into downtime and costly repairs. For instance, a digital twin of a production line machine can provide insights into its functioning, enabling timely maintenance and reducing the risk of unexpected breakdowns.
This not only enhances the lifespan of the equipment but also optimizes productivity and reduces operational costs. The healthcare sector is another domain where digital twins are making significant strides.
They are used to create highly accurate digital replicas of human organs. These virtual models can simulate various scenarios. It enables medical professionals to analyze the potential outcomes of different treatment strategies without any risk to the patient.
For example, a digital twin of a patient’s heart can help doctors understand the impact of a particular drug or surgical procedure, leading to personalized treatment plans and improved patient outcomes.
Urban planning is yet another field that is reaping the benefits of digital twins. City planners and architects can create digital twins of entire cities, providing a comprehensive urban landscape view.
These digital models can simulate various scenarios, from traffic patterns to energy consumption and even the impact of natural disasters. This enables more informed decision-making, leading to sustainable and efficient urban development.
FAQ
What is the Main Benefit of a Digital Twin?
Digital Twin’s main advantage is its ability to predict future performance and detect potential issues before they occur, saving time and costs.
What Industries Can Benefit from Digital Twins?
Almost every industry can benefit from digital twins, including manufacturing, healthcare, urban planning, etc.
Are Digital Twins Expensive to Implement?
The digital twin’s implementing cost can differ based on the physical entity’s complexity and the required level of functionality. However, the return on investment can be significant due to the potential maintenance and efficiency improvement savings.
End Note
In conclusion, digital twins represent a significant advancement in digital transformation. Creating a virtual representation of physical entities allows for real-time monitoring, predictive analysis, and optimized performance.
As technology evolves continuously, the capabilities and applications of digital twins are expected to expand even further.