In today’s fiercely competitive global marketplace, manufacturing enterprises are constantly seeking avenues to improve their operations and gain a competitive edge. Among the key factors that dictate success in the manufacturing sector, production efficiency reigns supreme. Production efficiency is the measure of how effectively resources are utilized in the manufacturing process to maximize output while minimizing costs and waste.
It serves as a critical metric for gauging the effectiveness of manufacturing systems, playing a pivotal role in determining profitability, customer satisfaction, and overall business sustainability.
The pursuit of production efficiency in manufacturing is driven by the overarching objective of achieving optimal performance. By optimizing production processes, manufacturers can achieve higher throughput, reduce lead times, enhance product quality, and ultimately deliver goods to market faster and at a lower cost.
However, attaining production efficiency is no simple task. It requires a multifaceted approach encompassing various elements, including process optimization, resource utilization, technology integration, and continuous improvement.
Throughout this essay, we will examine the key components of production efficiency, ranging from effective production planning and scheduling to streamlined supply chain management. We will explore the role of automation, data analytics, and advanced technologies in enhancing productivity and reducing waste. Additionally, we will delve into the importance of fostering a culture of continuous improvement and employee engagement to drive innovation and efficiency gains.
So without any more detours, let’s dive into what is production efficiency in manufacturing and how to achieve it.
Contents
What is Production Efficiency?
Production efficiency refers to the extent to which resources, such as labor, materials, and machinery, are utilized effectively in the manufacturing process to generate the maximum possible output while minimizing waste and costs. It is a measure of how well a manufacturing system or operation performs in terms of optimizing production and utilizing available resources efficiently.
At its core, production efficiency embodies the concept of achieving more with less. It aims to strike a balance between output quantity and quality, ensuring that the manufacturing process operates at its highest potential while maintaining or enhancing product standards. By maximizing output while minimizing resource consumption and waste, production efficiency enables manufacturers to improve profitability, competitiveness, and customer satisfaction.
Key Elements of Production Efficiency:
In practice, production efficiency encompasses several key elements:
1. Resource Utilization: It involves making the most effective use of available resources, including labor, raw materials, energy, and equipment. By minimizing idle time, reducing downtime, and ensuring optimal utilization, manufacturers can extract maximum value from their resources.
2. Minimizing Waste: Waste reduction is a vital aspect of production efficiency. This includes minimizing material waste, energy waste, and time waste through lean manufacturing principles and continuous improvement practices. By eliminating or reducing waste, manufacturers can enhance efficiency, reduce costs, and improve sustainability.
3. Process Optimization: Production efficiency involves analyzing and optimizing each step of the manufacturing process to eliminate bottlenecks, reduce cycle times, and enhance overall productivity. This may involve streamlining workflows, improving equipment performance, implementing automation, or reconfiguring production layouts to achieve optimal efficiency.
4. Quality Control: Ensuring high product quality is an integral part of production efficiency. By implementing robust quality control measures, manufacturers can reduce rework, scrap, and customer returns, leading to improved efficiency and customer satisfaction.
5. Continuous Improvement: Production efficiency is an ongoing journey rather than a one-time achievement. Continuous improvement initiatives, such as Kaizen or Six Sigma, play a vital role in driving efficiency gains by fostering a culture of innovation, problem-solving, and employee engagement.
By prioritizing production efficiency, manufacturers can enhance their operational performance, maintain a competitive edge, and adapt to changing market demands. It allows them to achieve higher productivity, lower costs, faster time to market, and ultimately deliver products that meet or exceed customer expectations. Through a combination of strategic planning, process optimization, and a commitment to excellence, manufacturers can unlock the full potential of their manufacturing operations and thrive in today’s dynamic business landscape.
How to Calculate Production Efficiency?
The formula for calculating production efficiency can vary depending on the specific context and industry. However, a commonly used formula for calculating production efficiency is:
Production Efficiency = (Actual Output / Maximum Possible Output) x 100%
In this formula:
- Actual Output refers to the actual number of units or products produced within a given timeframe.
- Maximum Possible Output represents the maximum achievable number of units or products that could be produced within the same timeframe, assuming ideal conditions and full utilization of resources.
By dividing the actual output by the maximum possible output and multiplying the result by 100%, the formula expresses production efficiency as a percentage. This percentage indicates how effectively the manufacturing process is utilizing resources and achieving its maximum potential output.
It is important to note that this formula provides a simplified representation of production efficiency and may not capture all factors that can influence efficiency in a complex manufacturing environment. Additionally, different industries and production systems may have their own unique formulas or metrics to assess production efficiency
Benefits of Production Efficiency:
Production efficiency brings numerous benefits to manufacturing enterprises. Here are some key advantages:
- Increased Productivity: Production efficiency maximizes the output achieved with the available resources, resulting in increased productivity. By optimizing processes, reducing downtime, and eliminating waste, manufacturers can produce more goods in the same amount of time, ultimately boosting overall productivity levels.
- Cost Reduction: Efficient production methods often lead to cost savings. By eliminating waste, reducing rework, and optimizing resource utilization, manufacturers can minimize production costs, such as labor, materials, and energy. This cost reduction directly contributes to improved profitability and competitiveness in the marketplace.
- Improved Quality: Production efficiency is closely tied to product quality. By implementing efficient processes and quality control measures, manufacturers can reduce defects, errors, and customer complaints. Higher quality products result in increased customer satisfaction, brand loyalty, and a reduced need for costly rework or returns.
- Shortened Lead Times: Efficient production systems enable manufacturers to reduce lead times, which is the time taken from order placement to product delivery. By streamlining processes, minimizing bottlenecks, and optimizing workflows, manufacturers can respond to customer demands more quickly, gaining a competitive advantage in the market.
- Enhanced Customer Service: Production efficiency allows manufacturers to meet customer demands promptly and effectively. With faster lead times, higher quality products, and improved reliability, manufacturers can provide exceptional customer service. This leads to increased customer satisfaction, repeat business, and positive word-of-mouth referrals.
- Increased Competitiveness: In today’s global marketplace, competitiveness is vital for the success of manufacturing enterprises. Production efficiency equips manufacturers with a competitive edge by enabling them to offer products at a lower cost, with shorter lead times, and with higher quality compared to their competitors. This positions them favorably in the market and enhances their chances of success.
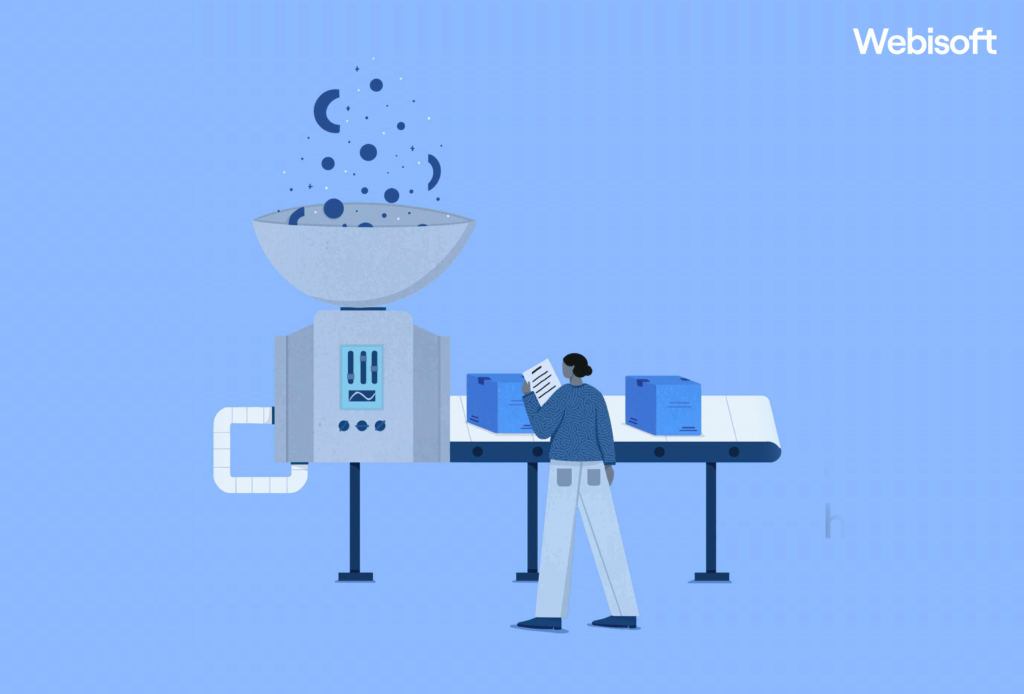
Ways to Achieve Production Efficiency
Achieving production efficiency requires a comprehensive approach that encompasses various strategies and practices. Here are several key ways to achieve production efficiency in manufacturing:
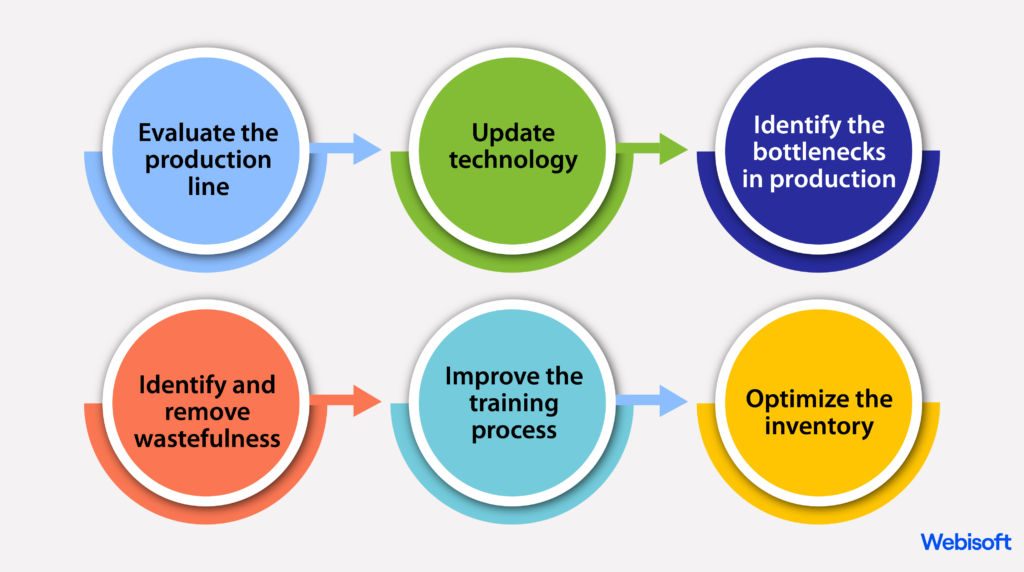
Process Analysis and Optimization
Conduct a thorough analysis of the production process to identify bottlenecks, inefficiencies, and areas for improvement. Utilize techniques such as value stream mapping to visualize the flow of materials and information and identify opportunities for streamlining and eliminating waste. Optimize workflows, rearrange production layouts, and implement lean manufacturing principles to improve process efficiency.
Advanced Technology Integration
Embrace technology to automate and optimize manufacturing processes. Implement advanced machinery, robotics, and automation systems to improve accuracy, speed, and consistency. Utilize data analytics and real-time monitoring to gather insights, identify patterns, and make data-driven decisions. Integrated systems such as Enterprise Resource Planning (ERP) software can facilitate efficient resource allocation, inventory management, and production planning.
Effective Production Planning and Scheduling
Develop robust production plans and schedules that align with customer demand and optimize resource utilization. Utilize forecasting techniques to anticipate demand fluctuations and adjust production levels accordingly. Implement efficient scheduling practices to minimize idle time, reduce changeover times, and maximize equipment utilization.
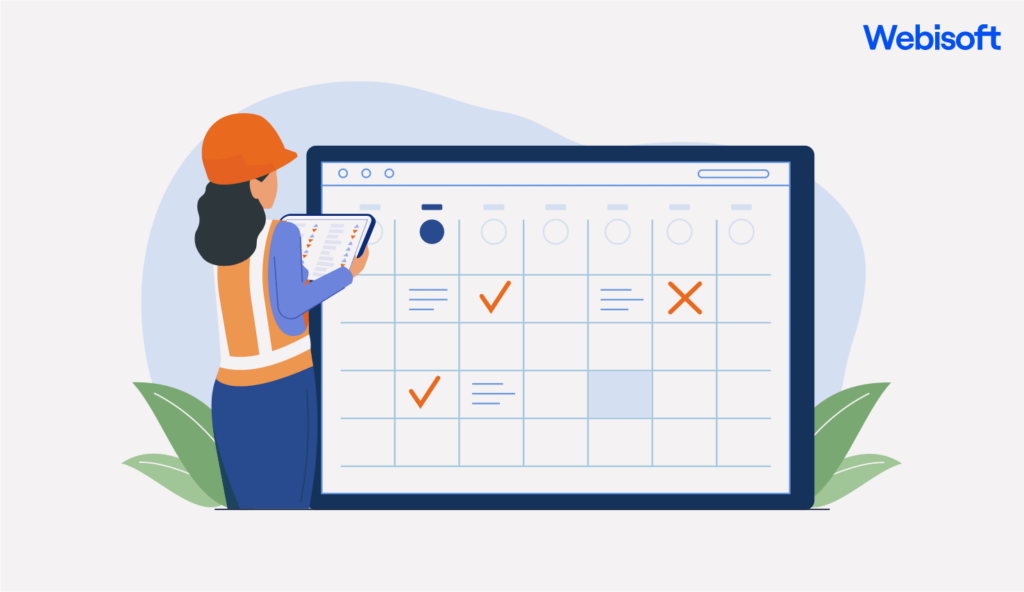
Supply Chain Collaboration and Optimization
Collaborate closely with suppliers and customers to optimize the supply chain. Establish strong relationships, share information, and implement efficient procurement and inventory management practices. Implement just-in-time (JIT) or lean supply chain principles to reduce inventory carrying costs, improve order fulfillment, and minimize waste.
Continuous Improvement and Employee Engagement
Foster a culture of continuous improvement within the organization. Encourage employees at all levels to identify and implement efficiency-enhancing ideas. Implement methodologies such as Kaizen, Six Sigma, or Total Quality Management (TQM) to drive continuous improvement initiatives. Provide training and development opportunities to empower employees and enhance their skill sets.
Quality Control and Waste Reduction
Implement robust quality control measures throughout the production process. Utilize statistical process control techniques to monitor and maintain product quality. Implement error-proofing methods, such as poka-yoke, to prevent defects. Focus on waste reduction by adopting practices like 5S (Sort, Set in Order, Shine, Standardize, Sustain) and Total Productive Maintenance (TPM) to eliminate equipment failures and maximize uptime.
Continuous Learning and Adaptation
Stay updated with industry trends, emerging technologies, and best practices in production efficiency. Encourage a learning culture within the organization and invest in employee training and development programs. Continuously evaluate and adapt production processes, technologies, and strategies to stay agile and responsive to market changes.
Frequently Asked Questions
What is production efficiency?
Production efficiency refers to the extent to which resources are effectively utilized in the manufacturing process to achieve maximum output while minimizing waste and costs.
How can production efficiency be measured?
Production efficiency can be measured using various key performance indicators (KPIs) such as overall equipment effectiveness (OEE), cycle time, scrap rates, production yield, and inventory turnover. These metrics help assess the effectiveness of production processes and identify areas for improvement.
How can technology contribute to production efficiency?
Technology plays a crucial role in production efficiency by automating processes, enhancing accuracy and speed, enabling real-time monitoring and data analytics, improving resource utilization, and facilitating seamless integration of different systems and operations.
Is production efficiency a one-time achievement or an ongoing process?
Production efficiency is an ongoing process rather than a one-time achievement. It requires continuous evaluation, adaptation, and improvement to stay aligned with changing market dynamics, technological advancements, and customer expectations.
Conclusion
By embracing production efficiency, manufacturers can unlock a multitude of benefits. Increased productivity, cost reduction, improved product quality, shortened lead times, enhanced customer service, increased competitiveness, sustainability, and improved employee morale are among the rewards that await those who strive for efficiency.
As the manufacturing landscape continues to evolve, the pursuit of production efficiency becomes increasingly crucial. By striving for efficiency, manufacturers can not only survive but also thrive in a highly competitive marketplace, meeting customer expectations, and driving sustainable growth.
In the dynamic world of manufacturing, where every minute and resource count, production efficiency is the compass that guides enterprises towards optimal performance. It is the catalyst that propels manufacturers to surpass their competitors, delight customers, and solidify their position as industry leaders.